Scope of Application
1. Non-combustible high concentration (BOD, COD) wastewater, waste liquid, waste acid, waste alkali, etc;
2. Combustible waste liquid, waste solvent, waste PCB, etc;
1. Good pulverization effect, it adopts forth generation pulverization device with good burning effect;
2. Without second pollution, low nitrogen burning technology, without any smoke, smell or deleterious gas;
3. High safe performance, ultraviolet supervising system and complete warning system without the danger of explosion;
4. Low malfunction rate, imported parts, dual-loop system, high quality and long lifetime;
5. Good disposal effect with low cost for waste oil, waste liquid, waste solvent and organic waste gas at the same time.
Hazardous waste handling capacity: 10-10000kg/h
Yongxing Kunpeng
The main waste to be treated in this project is organic waste liquid, which enters the waste liquid storage tank in the incineration unit through various process pipelines for storage, and the incineration device processes 2 waste liquids in total. The waste liquid in the waste liquid storage tank is pumped to the waste liquid spray guns on the top of the primary combustion chamber and the bottom of the secondary combustion chamber. Under the action of compressed air, the waste liquid enters the incinerator after being atomized. Under the action of oxygen-supplementing wind, the waste liquid is fully burned in the incinerator. The ash enters the slag discharger and is finally transported to the silo for storage. The flue gas enters the secondary combustion chamber again, and combustible gases such as long and short chain hydrocarbons and CO in the flue gas are further turbulently mixed under the torsion of the secondary air, and can be fully exhausted under the "3T+E" environment. Combustion will completely decompose dioxin-like substances. Under normal circumstances, the furnace temperature in the combustion chamber is above 1100°C, and the designed total residence time is above 2 seconds. The organic hazards in the flue gas are completely destroyed and transformed into CO2, SOX, and HCl gases to achieve the purpose of complete sterilization, disinfection, and deodorization.
The high-temperature flue gas that is fully burned in the secondary combustion chamber directly enters the waste heat steam boiler (membrane wall boiler) to cool down to about 500°C. The inlet of the steam boiler is equipped with a SNCR denitrification system (in-furnace denitrification) interface to remove nitrogen and oxygen. compound. The flue gas then enters the quenching deacidification tower, where it is sprayed with dilute lye, and the temperature is lowered to about 200°C within 1 second to prevent the re-production of dioxins. Then, hydrated lime and activated carbon are sprayed into the dry spray tower to remove HCl, SO2, HF and other acid gases in flue gas and remove heavy metals and dioxins in flue gas. Then the flue gas enters the bag filter to remove particulate matter such as fly ash and waste activated carbon. The purified flue gas enters the flue gas reheater through the induced draft fan for heat exchange, and then enters the packing spray tower to further purify the acidic components and dust, and wash the cooled flue gas. The gas then enters the front-end flue gas reheater coil for heat exchange and whitening. Finally, the flue gas that reaches the standard is discharged at high altitude through the chimney.
Flow chat
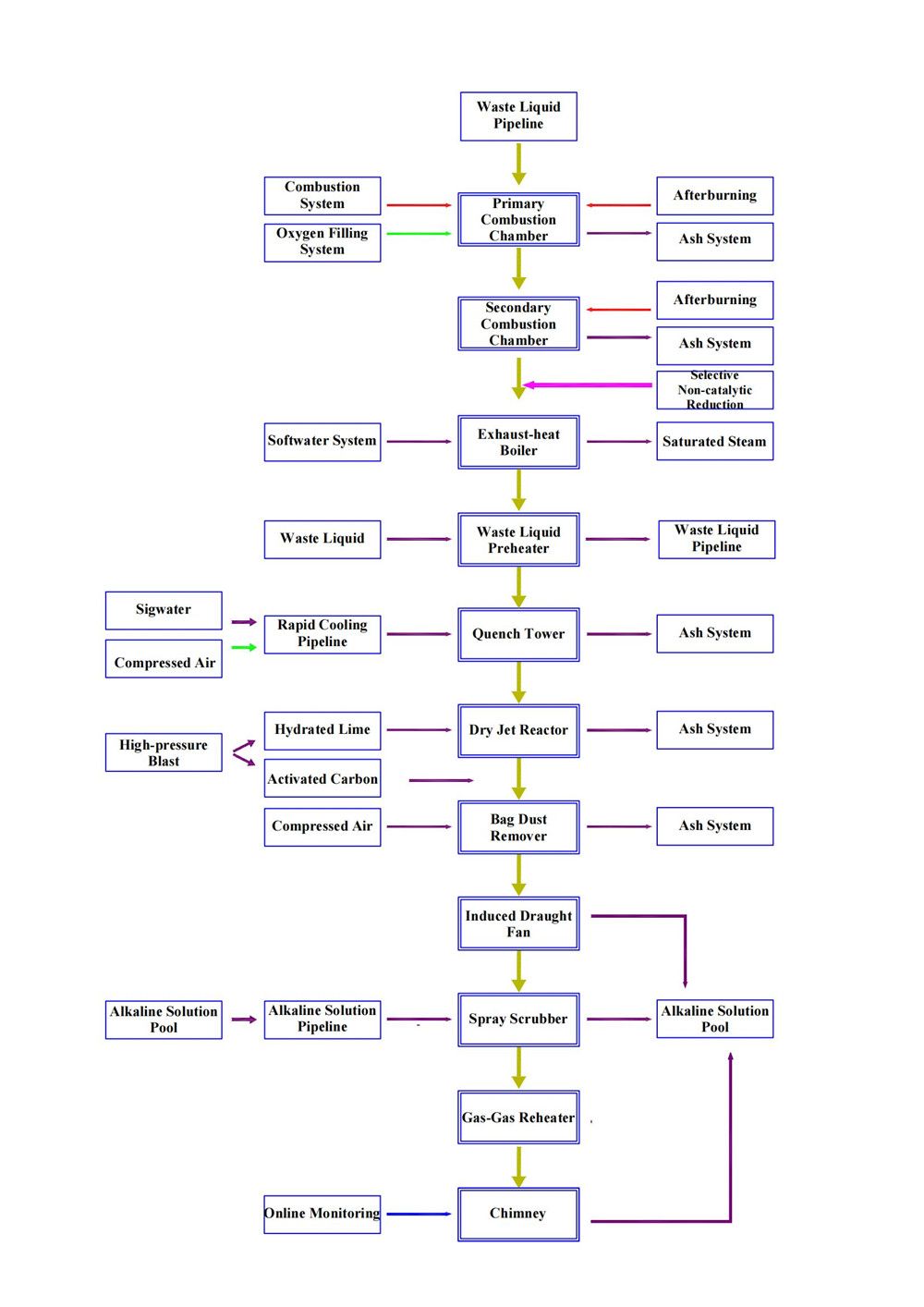
Reviews
There are no reviews yet.